First of it all, thanks Steve,and to all trolls sharing knowledge here.Whitout this forum I'll never attempt this project!
I'm not presenting any finished machine nor satifiying recordings, just some test I made and will probably be for long time work in progress.I´ve got some experience in speaker repair and assorted windings, so I decide to add feedback coils to tweeters.But I ruined the coil while upgrading the magnet to neodimyum so,WTF, I'll wind the whole thing new.I'm not a big paper coil former fan, but is the lightest option for me, an after all the paper is just something to absorb varnishes to improve its properties.
All coils are 16mm, diameter. The drive have 50 turns of awg 42,in two layers, one inside the former and the other outside it.This avoid one of the layers to sweet in an inferno between outer layer and former,and also avoid deformations for uneven dilatation of different materials.
The two feedback coils(per channel) are winded clockwise one, and anticlockwise the other, for cancelling the EMF from drive,and inmersed in opposite magnetic fieds,for adding the signal generated by movement.(Exactly the same way the humbacking guitar pick ups cancel hum),one is 10 mm above the drive (I mean its centre) an has 30 turns of AWG 34.The other is 16 mm. above the drive and has 55 turns of the same wire, but winded the other direction.
I used thinner wire,but it was a nigthmare to solder, so I go with this for now.It had 50 ohm, and now it has 21,but any way it's outpus is usable for the pourposes.It can be also 110/60 but prefer to keep the inductance low,to avoid weirder phase matches with the program to be mixed.
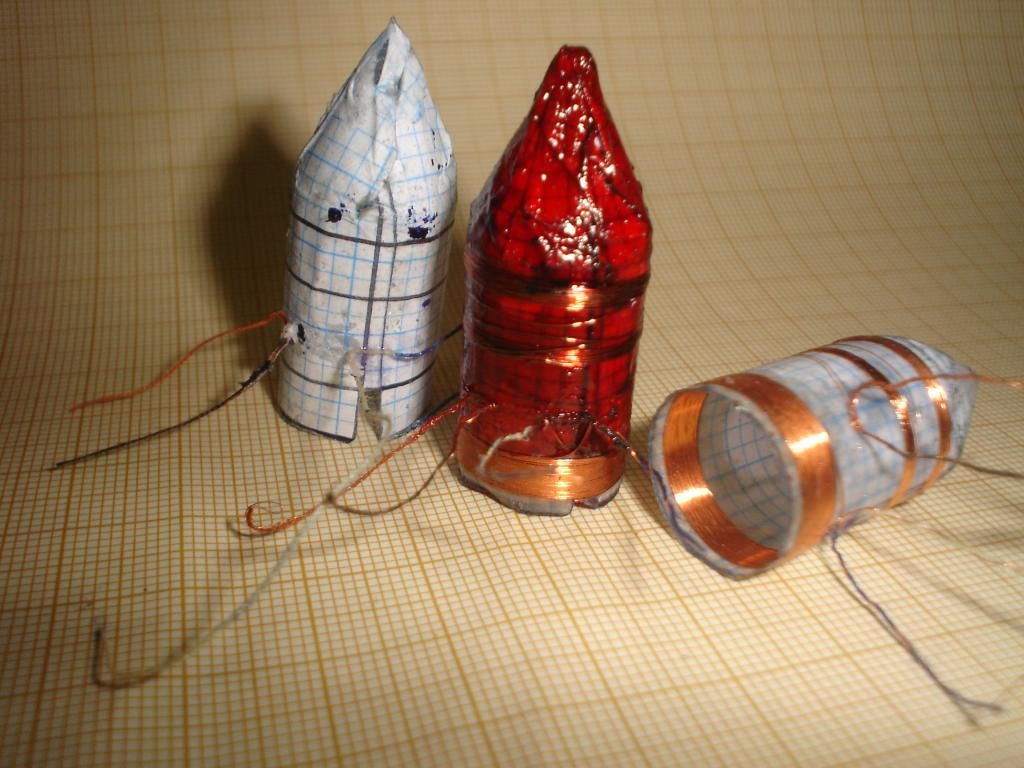
I used silicone for damping,I think tweeters (and way more full ranges!)have too little damping for this application.I damp it like there were no tomorrow. .on the polepice of the speaker,there is a cylinder with a magnet glued at its end,to polarize the feedback coils.I also made a metalic ring for closing the magnetic circuit,but it didn't behave as in computer simulation, it gave clearer and stronger signal without it! (???????)Have a look at the assembly(Only one coil is on):
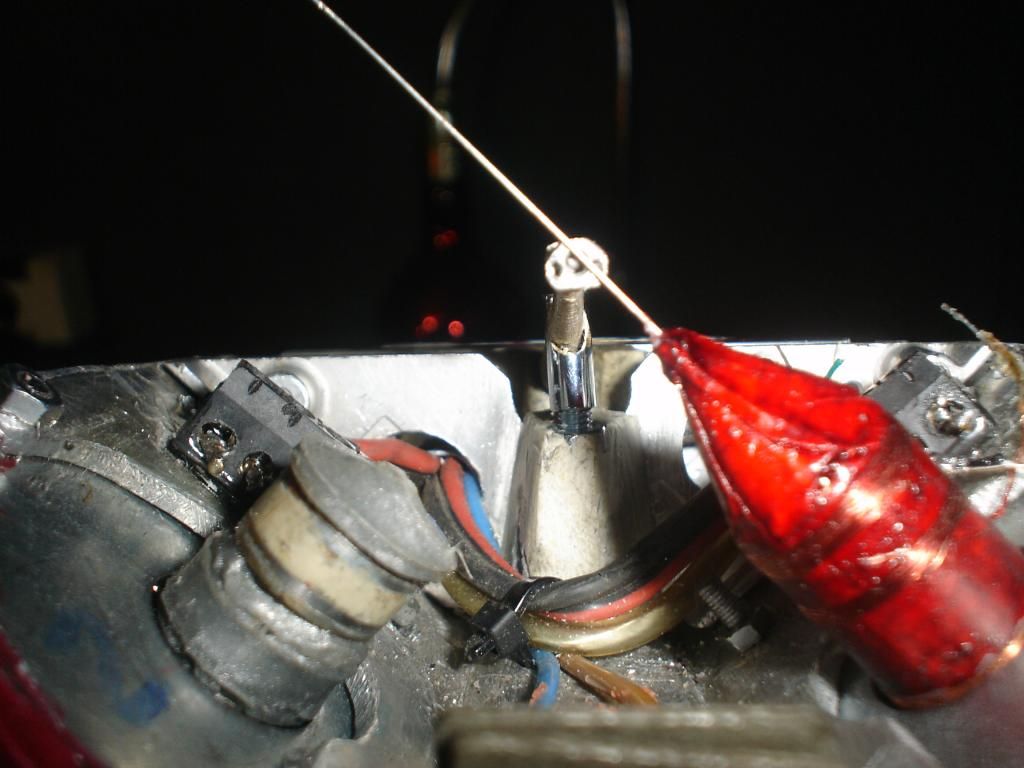
I did'nt build a proper mixing console yet,untill that I'm using a dj mixer(After making shure the feedback phase is inverted respect to the program) and the thrashy PC I'm using has the worst sound card I ever heard,in its mother-f***n-board.it's hermaphrodithe test gave a rollercoaster response. So no spectrum analyse possible.But a sweep up with audacity gives a clue.too many things to do next week!....
Here¡s a video of the test: I don't know what's to blame for the treble fade out, maybe the pc card, maybe the head capabilities(probably this) or the phase mismatch,(The feedback signal has a delay respect to the program more noticeable in the high pitch). Maybe I have to add fancy things in the feedback loop,(op-amp style)
If you are curious abut the rest of the machine...Well here¡s a picture of the whole thing.
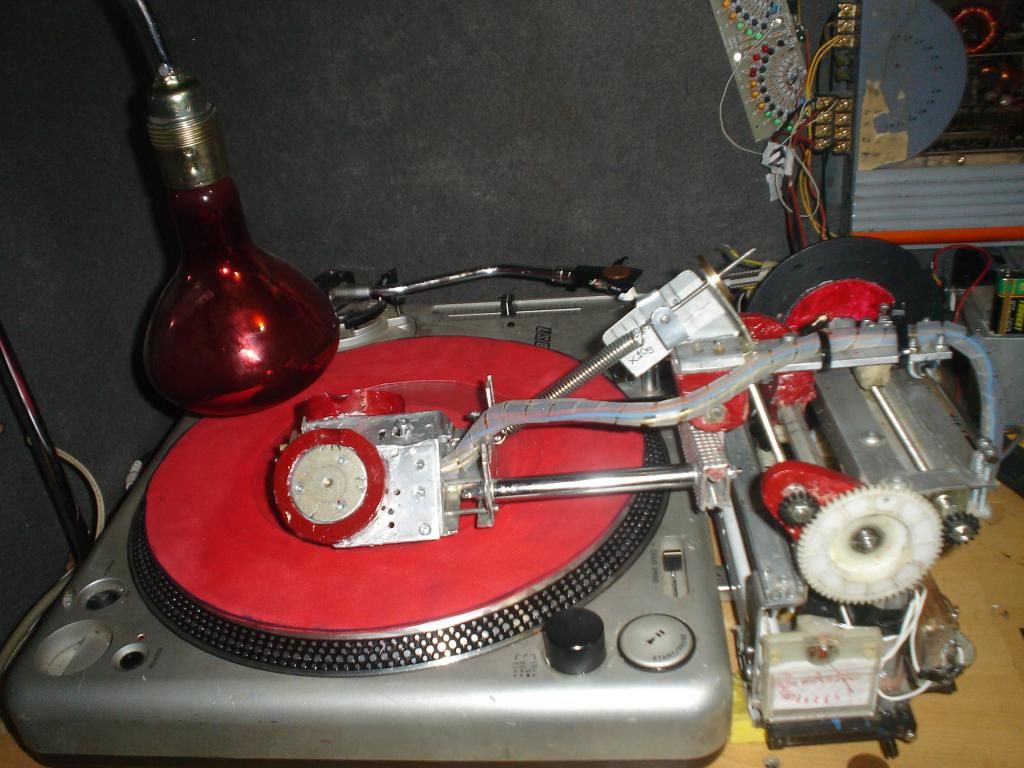
Not proud of it.It has some design nonsenses because I change my mind during the process(too long arm, tiny feedscrews...)It was intended for a home made turntable,but I found a cheap direct drive BST PR 436.At the end it barely has torque for embossing under 150 grs.
So, after collecting some data,I'll make everything new!
Cheers!